What is the quality assurance process used by hospital and diagnostics distributors?
- mahendrago4distrib
- May 15, 2024
- 4 min read
1. Regulatory Compliance
Ensuring adherence to regulatory standards is the cornerstone of QA in the healthcare sector. Distributors must comply with regulations set by bodies such as the Food and Drug Administration (FDA) in the United States, the European Medicines Agency (EMA) in Europe, and other local regulatory authorities. These regulations cover various aspects including manufacturing practices, product storage, transportation, and handling procedures. Compliance is verified through regular audits and inspections by regulatory bodies Hospital and diagnostics distributors.
2. Vendor and Supplier Qualification
A critical component of the QA process is the qualification of vendors and suppliers. Distributors conduct rigorous evaluations of potential suppliers to ensure they meet the necessary quality standards. This involves reviewing their manufacturing processes, quality control measures, and compliance with regulatory requirements. A robust vendor qualification process reduces the risk of receiving substandard or non-compliant products.
Hospital and Diagnostics Manufacturers
Hospital and diagnostics manufacturers play a crucial role in the healthcare supply chain by producing essential medical devices, diagnostic equipment, and other healthcare products. These manufacturers must adhere to strict quality standards and regulatory requirements to ensure their products are safe and effective. They implement comprehensive quality management systems (QMS) that encompass design control, production processes, and rigorous testing protocols. Innovation and research are central to their operations, enabling the development of advanced medical technologies that improve patient care. Additionally, manufacturers collaborate closely with healthcare providers to tailor products to meet specific clinical needs and enhance overall healthcare outcomes.
3. Incoming Product Inspection
Upon receiving products, distributors perform thorough inspections to verify their quality and compliance with specifications. This inspection includes checking for damage, verifying product labeling, and ensuring that accompanying documentation such as certificates of analysis and compliance are in order. Advanced techniques like barcode scanning and automated inventory systems can enhance the accuracy and efficiency of this process.
4. Storage and Handling
Proper storage and handling are vital to maintaining the quality and efficacy of medical products. Distributors must ensure that storage facilities comply with specific temperature and humidity requirements, which is particularly important for sensitive items such as pharmaceuticals and diagnostic reagents. Regular monitoring and maintenance of storage conditions are conducted to prevent degradation of products. Additionally, handling procedures are designed to minimize the risk of contamination or damage during transit.
5. Quality Control Testing
In-house quality control (QC) testing is a crucial step in the QA process. Distributors often have laboratories equipped to perform various tests on products to verify their quality. This can include chemical analysis, microbiological testing, and physical inspections. QC testing helps ensure that products meet the required specifications before they are distributed to healthcare providers.
6. Documentation and Record Keeping
Accurate documentation and record keeping are essential components of the QA process. Distributors must maintain detailed records of all QA activities, including vendor qualifications, product inspections, storage conditions, and QC test results. These records are essential for traceability, enabling distributors to track products through the supply chain and respond effectively to any quality issues or recalls.
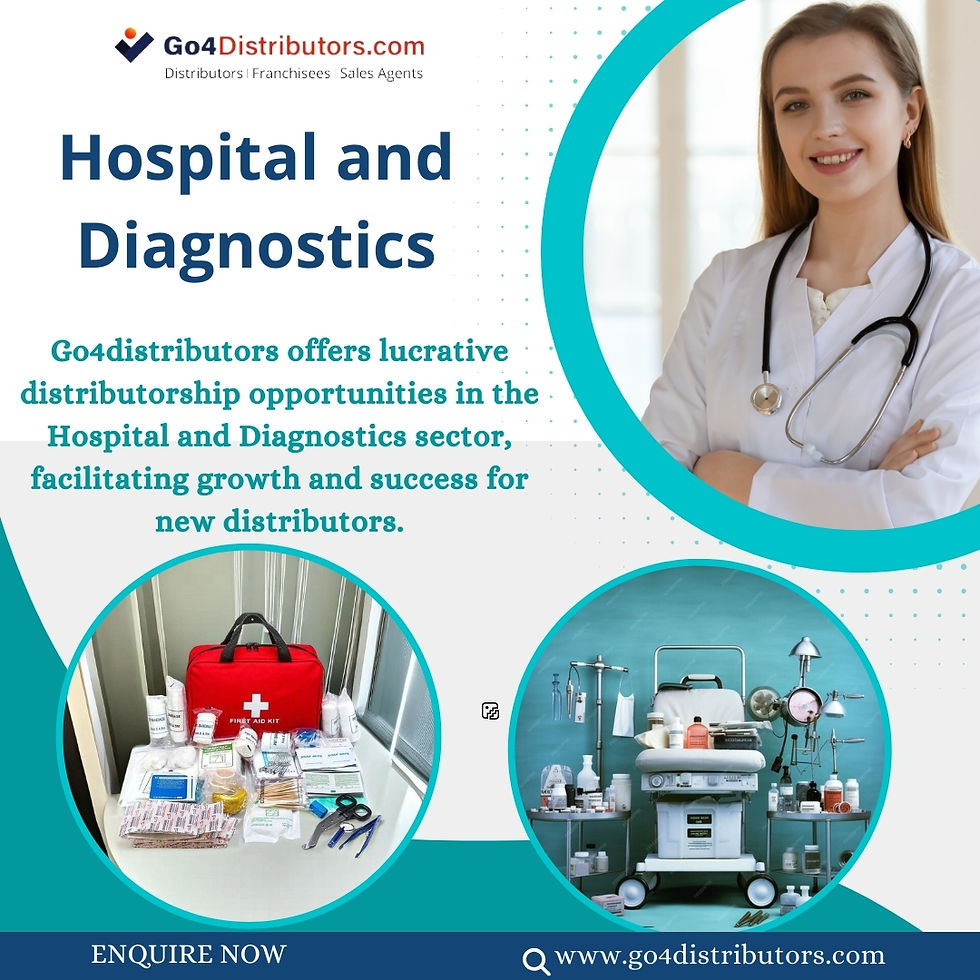
Hospital and Diagnostics Wholesalers
Hospital and diagnostics wholesalers act as intermediaries between manufacturers and healthcare providers. They are responsible for the bulk distribution of medical products, ensuring that hospitals, clinics, and diagnostic centers have timely access to essential supplies. Wholesalers maintain large inventories and utilize efficient logistics networks to manage the rapid delivery of products. They also ensure compliance with quality and safety standards, conducting regular inspections and audits of their storage facilities. By offering a wide range of products from multiple manufacturers, wholesalers provide healthcare providers with a reliable and convenient source for their procurement needs, ultimately supporting the smooth operation of healthcare services.
7. Training and Education
Ensuring that staff are well-trained and knowledgeable about QA procedures is critical. Distributors provide ongoing training programs to educate employees on the latest regulatory requirements, quality control techniques, and best practices in handling and storage. Continuous education helps maintain a high standard of quality and ensures that all staff members are competent in performing their roles.
8. Risk Management and Continuous Improvement
A proactive approach to risk management involves identifying potential quality risks and implementing measures to mitigate them. This can include conducting regular risk assessments and developing contingency plans for addressing quality issues. Additionally, the QA process is dynamic, with continuous improvement practices in place. Distributors regularly review and update their QA procedures based on feedback, audit results, and advancements in technology and best practices.
9. Customer Feedback and Complaint Handling
Customer feedback is an invaluable resource for quality assurance. Distributors establish systems for collecting and analyzing feedback from hospitals and healthcare providers regarding the quality of products and services. Complaints are investigated promptly, and corrective actions are implemented to prevent recurrence. This feedback loop helps distributors identify areas for improvement and ensures customer satisfaction.
Go4Distributors: Facilitating Connections in India
Go4Distributors is a specialized platform designed to bridge the gap between manufacturers and distributors in India. By offering a comprehensive directory and matchmaking services, Go4Distributors helps manufacturers find reliable distribution partners who can effectively market and distribute their products. For distributors, the platform provides access to a wide array of manufacturers, facilitating the selection of quality products that align with their business goals. Go4Distributors enhances the efficiency of the supply chain by streamlining the search and selection process, ensuring that manufacturers and distributors can forge strong partnerships. This, in turn, contributes to better availability of medical products across the healthcare sector in India.
Visit:- Appoint Distributors
Yorumlar